PRRS: Winter is Coming
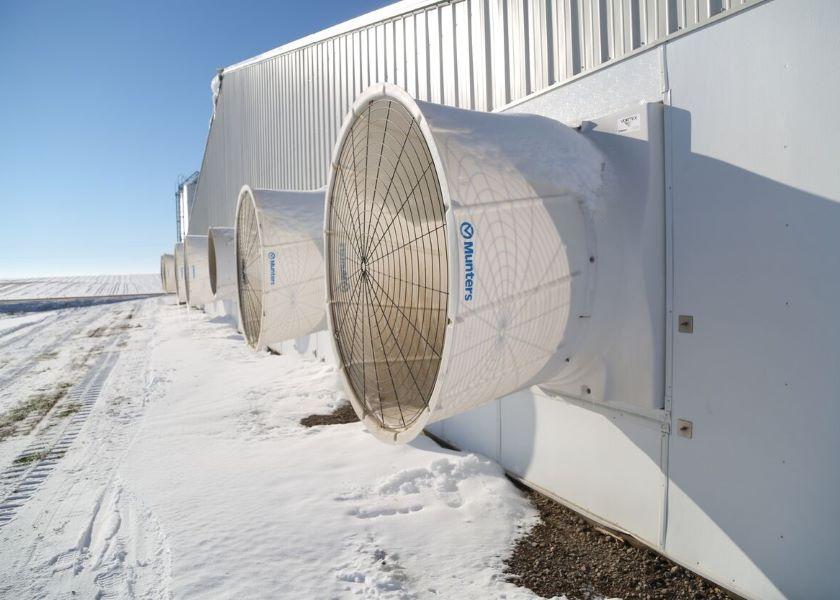
How prepared are your farm and team for PRRS season? Ready or not, peak disease transmission season has arrived in the swine industry. Porcine reproductive and respiratory syndrome (PRRS) is a frustrating and complicated disease. It demoralizes our teams at all levels, from the ownership to the newest technicians on the farm.
We have numerous tools to help with PRRS prevention, control, stabilization and elimination, but none of them individually represent a “silver bullet.” Regardless of how challenging PRRS can be, we have to face the brutal reality that production systems that don’t effectively manage PRRS cannot be competitive in today’s marketplace. As such, we have to position our PRRS management resources strategically to optimally battle PRRS while being realistic that there will be times PRRS has the upper hand at our farm.
Where to Start?
Biosecurity. Plain and simple, preventing wild-type PRRS infection is the best possible outcome for a PRRS management program. Good biosecurity programs involve good biosecurity plans. Note the plural form of the term “plans” – PRRS can enter the farm through a number of different avenues and we must have specific biosecurity plans for each of these potential routes of introduction. While PRRS is infamous for its ability to “fly” into the farm via aerosols, the reality is very specific climatic conditions are required to facilitate PRRS transmission via aerosols. It’s possible on specific days, but even in the winter, most days in most pig-producing regions don’t have the appropriate climatic conditions to facilitate PRRS transmission via aerosols.
Let’s start by focusing on the areas PRRS can enter the farm every day.
People, supplies, equipment and animal introductions represent huge areas of opportunity for PRRS introduction. Everything that comes into our farm can serve as a fomite, and when contaminated, bring PRRS into our farm. Fomite management starts with defining “clean and dirty lines” (CDL). As my good friend Dr. Mark Thompson of The Maschhoffs taught me: Define and Defend these areas.
The first CDL most of us encounter when coming to a farm is the bench entry. This area represents a CDL meant to remove our personal items most likely to be contaminated, specifically our personal shoes we wore to the farm. It is critical we remove our shoes and swing our feet over the bench to the “clean” side without contaminating our socks. While this seems obvious, it’s very common to find evidence at the bench that indicates our farm teams don’t understand this concept. If you see shoes that are located farm away from the bench, you know those people had to contaminate their socks on the dirty side of the bench prior to crossing it. Shoe direction at the bench can also be a good tip about execution. If you see shoes facing the bench (toe side pointed toward the bench), that can also be a good indicator that there’s a coaching opportunity for that farm.
Benches represent a wonderful opportunity to teach people about the concepts of the CDL, including:
1. There is a clean side and a dirty side.
2. We don’t want items that contact the dirty side to cross onto the clean side.
3. For items that must come across the CDL onto the clean side, some sort of sanitation step should always occur prior immediately prior to crossing.
Supply and equipment entry represent our next key area of biosecurity focus. As a rule of thumb, supplies and equipment coming into the farm should always be new and have never been on another pig farm. Historically, the pig industry has used “disinfection rooms” with “foggers” to aerosolize chemical disinfectant as our primary means of supply and equipment entry. Through a series of research projects, Dr. Jim Lowe and his team at the University of Illinois have taught us that the aerosolization of chemical disinfectant represents an incomplete way to apply disinfectant to all surfaces of our supplies and equipment. Even when we work to space out supplies and place them on open bottom metal shelving, we still observe very poor disinfectant coverage of the sides of our supplies and equipment that aren’t immediately facing the fogging machine. Simply put, relying solely on a fogging machine to disinfect your supplies and equipment is not going to result in complete sanitation of these incoming items.
Fortunately, sanitation options exist outside of chemical disinfection and even better, they’re easy for farm teams to execute. Many farms have transitioned to heated downtime as a means of supply introduction. We often use the same disinfection rooms that historically fogged our incoming items, except we had heat (if needed) to warm this room consistently to room temperature and place our incoming supplies in these rooms for seven days before entering them into the farm. Compliance is easier as we don’t have to space out all incoming supplies, stacking them in the room is acceptable. We obviously still need to use chemical disinfection on perishable items as well as emergency supplies needed in the farm right away, but I’ve found that compliance with manual spraying of chemical disinfectant on these “one off” introductions is much better than asking someone to manually disinfect every item that comes into the farm.
Although animal transport vehicles and mortality handling equipment don’t come into the farm, I would be remiss to not include them in a discussion about PRRS prevention. Let’s start with animal transport vehicles. These vehicles and their drivers represent an extremely unique and dangerous risk to our pig farms – they have to come to the farm, and we know they go to other farms and animal concentration points which potentially have PRRS-positive pigs. At the farm, we always consider the vehicles and drivers “dirty” and flawless execution of the CDL that separates the clean side of the farm from the dirty side of the vehicle is absolutely critical.
It’s easy for me to write an animal loading SOP that directs farm workers to load the truck without crossing the CDL, but I’ve loaded a lot of trucks in my life and I have the practical experience to understand that while the protocol is easy to write, it’s extremely difficult to execute. Asking our farm teams to load 1,600 weaned pigs onto a trailer in 10-degree Fahrenheit temperatures with a 30-mph wind blowing directly into the chute without having some compromise of the CDL is an unrealistic expectation.
As such, we lean on the principles of stages loading to create two CDLs. The first CDL is always at the back of the livestock vehicle and the end of your chute. The second CDL is the next or gate you encounter as you move into the clean side of your farm. We station one farm employee between these two CDLs and this area is considered dirty during the loading process. This employee has dedicated equipment (sort boards and other movement tools) as well as segregated coveralls and boots to wear in this area. Immediately after we load pigs, the employee working in between the CDLs immediately washes and disinfects this area, again using equipment dedicated for only this purpose. When items from between these CDLs need to be removed from the farm we remove these outside, directly to the dirty area outside the farm.
Mortality handling equipment should follow the principles, with flawless execution of CDL at the mortality removal area being the focus. Ideally, we’d like to have an elevated platform to remove mortality across the CDL with the benefit of gravity helping move larger animals out of the farm. Where this option doesn’t exist, consider using a rope system where you place the mortality immediately next to the CDL, tie a rope around the leg of the mortality and throw the other end of the rope outside. The employees working on the dirty side of the CDL will access this other end of the rope and use it to pull the mortality across the CDL.
Don’t Forget Air Filtration
If you’re reading this article and feel satisfied that your farm and your team have all the above tools and processes in place, but you’re still frustrated with your PRRS introduction rate, let’s talk about air filtration. One of the more revolutionary tools the industry has developed – air filtration systems – are thanks to Dr. Satoshi Otake for his excellent work characterizing the risk of aerosol transmission as well as Dr. Scott Dee for his willingness to research and champion the early adoption of air filtration systems to mitigate this threat.
As with all new technologies, the cost of air filtration has come down and a tool once generally reserved for high-value assets such as boar studs is now often cost-effective to adopt for commercial sow farms in pig-dense locations. When coupled with positive-pressure ventilation systems, air filtration systems give the farm a reasonably user-friendly tool to mitigate the threat of PRRS virus entering via contaminated aerosols. I think the most important consideration with air filtration is doing a thorough evaluation of your other potential PRRS introduction risks. If you have gaps in people entry, supply and equipment entry, transportation biosecurity or mortality handling, we need to shore up those areas before investing in an air filtration system.
Specific to Your Farm
PRRS is complicated and frustrating, but if we optimize our biosecurity resources, we can expect good success in preventing PRRS introduction into our farm. Excellent benchmarking tools exist through the Morrison Swine Health and Management Program (MSHMP) to help compare your PRRS outbreak rate to your peers in the industry.
If you’re looking for information on how to improve your biosecurity going into this winter, hopefully this article gives you somewhere to start. Remember, biosecurity plans need to be specific to your farm – consult with your veterinarian about your ideas and work with them to define the optimal PRRS prevention plan for your team and operation.
More from Farm Journal's PORK:
Follow the Science to Beat PRRS 1-4-4, Lineage 1C
Biosecurity: Are We Adding Hazards Faster Than Control Measures?
What Do You Need to Pay Attention to Now Regarding Swine Health?